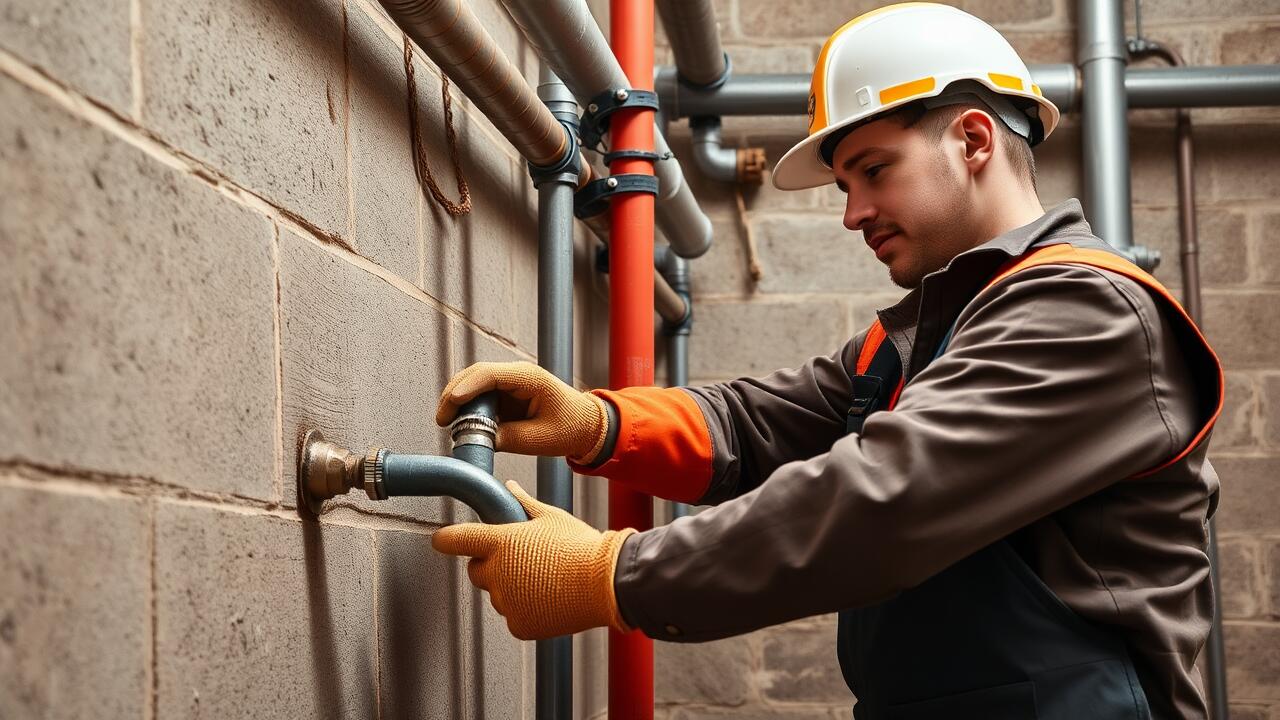
Quality Control Measures During Installation
Quality control measures during the installation of HDPE pipes are essential for ensuring durability and reliability. Regular inspections should be conducted throughout the process to verify that the installation meets industry standards. Personnel must be trained to recognize inconsistencies or defects in the materials. In Northridge, Los Angeles Pipe installation, adherence to specified guidelines can prevent costly repairs and disruptions, enhancing the overall performance of the infrastructure.
It is important to establish a clear protocol for quality checks at various stages of the installation. This includes monitoring the preparation of the trench, proper alignment of the pipes, and secure fittings. Documentation of each step in the process not only serves as a reference for ongoing projects but also supports compliance with local regulations. Regular communication among team members can help identify potential issues early on, making the installation more efficient and effective.
Ensuring Pipe Integrity and Performance
Ensuring the integrity and performance of HDPE pipes is crucial for a successful installation process, particularly in locations such as Northridge, Los Angeles. Regular inspections during the installation can help identify any issues that may compromise the pipe’s functionality. Utilizing appropriate testing methods to assess the strength and durability of the pipes before installation minimizes the risk of future failures. This proactive approach helps in maintaining optimal pressure levels and resistance to environmental stresses.
Proper jointing techniques are essential in securing the longevity of HDPE pipes. The fittings and connections must be installed according to industry specifications to prevent leaks and maintain system integrity. Training installation crews on these techniques can significantly improve overall performance. It is also beneficial to adhere to guidelines established by local codes to ensure that the HDPE pipes can withstand the specific conditions present in the Northridge, Los Angeles pipe installation.
Handling and Transportation of HDPE Pipes
Proper handling and transportation of HDPE pipes is crucial to maintaining their integrity and ensuring successful installation. These pipes, while sturdy, can be vulnerable to damage if not handled with care. Techniques such as using lifting equipment designed specifically for this type of material can help minimize the risk of bending or cracking. When storing pipes, stacking them horizontally and placing protective barriers between layers can prevent contact-related damages during both transport and installation.
In the context of Northridge, Los Angeles pipe installation, it is essential to follow local regulations and safety guidelines during the transport process. Transporting HDPE pipes requires consideration of weight distribution and road conditions to avoid shifting or rolling during transit. Using dedicated transport vehicles equipped with appropriate tie-downs will further safeguard against movement. These practices not only preserve the pipes' quality but also facilitate a smoother installation process when they arrive at the job site.
Best Practices for Safe Transport
When transporting high-density polyethylene (HDPE) pipes, maintaining their integrity is critical. Transport vehicles should be equipped with appropriate supports and cushioning to prevent movement and damage during transit. Proper strapping techniques can help secure the pipes against shifting, especially on uneven roads. In areas like Northridge, Los Angeles, where road conditions can vary, ensuring that pipes are adequately protected during transportation is vital to prevent cracks or deformities before installation.
Careful planning of the transport route also contributes to the safety of HDPE pipes. Drivers should be aware of any low-clearance areas, sharp turns, or rough terrain that could pose risks. Regular inspections of the transported materials can help catch any potential issues early. Proper documentation and adherence to local regulations for transporting construction materials will further enhance the safety process, ensuring that the integrity of pipes is maintained from the moment they leave the distributor until they reach the installation site.
Common Challenges Faced During Installation
Common challenges during HDPE pipe installation can vary depending on site conditions and project specifics. Uneven terrain and soil composition often pose significant difficulties. Additionally, weather conditions may affect installation, with rain or extreme temperatures impacting the performance of installation crews and the materials themselves. These factors can lead to delays and complications that require careful planning and management to avoid escalating costs.
Northridge, Los Angeles pipe installation projects frequently encounter obstacles related to existing infrastructure. Workers must navigate around utility lines, which can complicate positioning and installation techniques. Maintaining the proper alignment and avoiding damage to surrounding facilities is crucial. Awareness of these challenges enables teams to implement effective strategies while ensuring adherence to safety standards throughout the installation process.
Troubleshooting Issues with HDPE Pipes
Troubleshooting issues with HDPE pipes often requires a systematic approach to identify the source of the problem. Common issues include leaks, misalignment, or deformation of the pipes. Inspecting joints and connections is critical, as improper fusion or fitting can lead to significant complications. Regular monitoring during the installation process helps catch potential problems early, preventing costly repairs later.
In areas like Northridge, Los Angeles, pipe installation can encounter unique environmental challenges. Soil conditions may impact the stability of HDPE pipes, necessitating additional support or reinforcement. When issues arise, it is essential to assess the surrounding environment and consider factors such as temperature fluctuations and ground movement. By understanding these conditions, crews can implement solutions that ensure the longevity and effectiveness of the installation.
FAQS
What is High-Density Polyethylene (HDPE) pipe used for?
HDPE pipe is commonly used for various applications such as water distribution, wastewater management, and industrial piping due to its durability, flexibility, and resistance to corrosion.
What are the quality control measures for HDPE pipe installation?
Quality control measures include ensuring proper alignment and support, conducting pressure tests, and using certified materials to confirm that the pipes meet industry standards.
How should HDPE pipes be handled during transportation?
HDPE pipes should be handled with care to avoid damage, must be transported on flat surfaces, and should be secured to prevent movement. It is also important to avoid dragging the pipes to minimize abrasion.
What are some common challenges faced during HDPE pipe installation?
Common challenges include misalignment during installation, difficulties with fusion welding, and managing site conditions such as soil stability and moisture levels.
How can issues with HDPE pipes be troubleshot during installation?
Troubleshooting can involve checking for proper fittings, ensuring that joints are properly fused, and inspecting for any physical damage or deformation in the pipes. Regular monitoring during installation can also help identify problems early.